The use of virtual reality is becoming the new normal for the industry players and is progressively revolutionizing the product design and training stages. Will augmented reality revolutionize manufacturing processes as well? How far can these technologies be integrated into the production pipeline? Read the crossed points of view of Patrick BAERT, teacher and head of the virtual reality activity at the National Engineering School of Saint-Etienne (Enise), and Frédéric BORREL, head of virtual reality and augmented reality development at Volvo Renault Trucks.
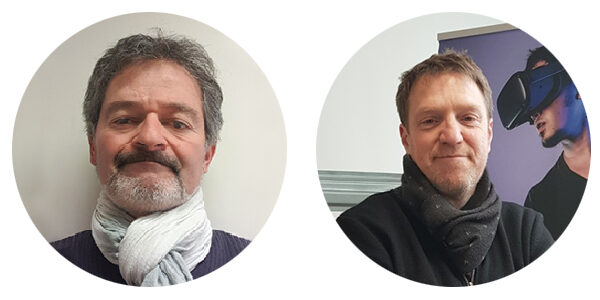
Patrick BAERT (left) and Frédéric BORREL (right)
How would you define virtual reality?
Patrick BAERT: It is a system that allows a user to be immersed in an artificial universe in which interactions are possible in real time with the environment that is displayed. The universe and the user interact together. Everything has been designed to generate actions. Virtual reality can be used for training, personal development or organizing team events, when employees are dispatched in different countries.
What is the difference with augmented reality?
Frédéric BORREL: With augmented reality, we will use other devices, such as connected glasses and display additional information in the field of vision of the operator. We also talk about mixed reality, which is a mixture of both and allows advance visualization at scale 1 via a 3D screen.
Patrick BAERT: The technology and purposes are different. With augmented reality, we visualize a natural environment, and we increase the reality of it with digital information on a phone, a tablet or connected glasses. The aim of virtual reality is to generate immersion, to transport the user into another universe. We must therefore believe in it, offer the most immersive experience. The user must be in control of this digital environment, whereas with augmented reality, he is more of an actor playing and being distracted by visual, sensory, and sound effects.
How do these new technologies make a difference in the development and design phase?
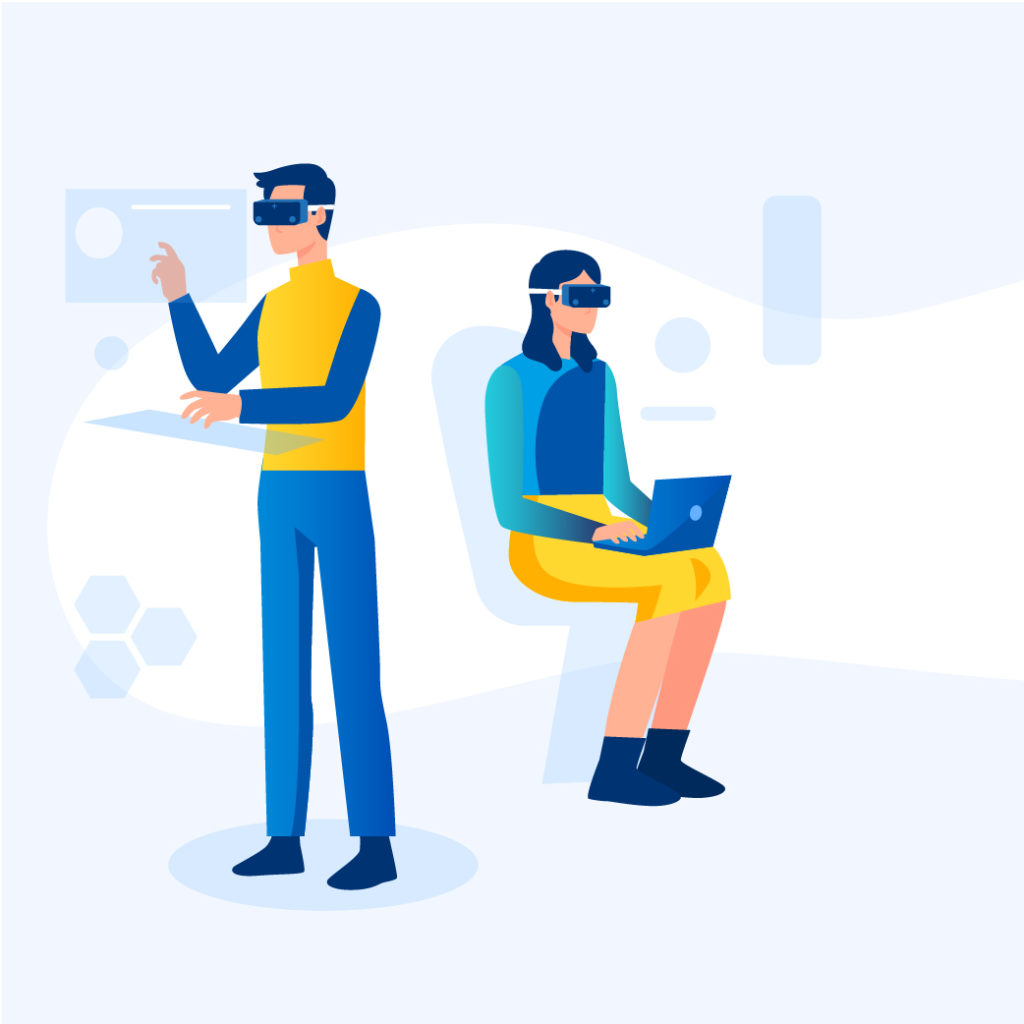
Patrick BAERT: Virtual reality can be used from the genesis of an idea to its realization. For example, it can be used for prototypes, working on a product’s size, its accessibility, its assembly, the posture of future operators, the manufacturing process. Virtual reality thus avoids long stages of development because we can work and iterate on a virtual prototype before making a physical prototype.
Frédéric BORREL: In the design phase, we can use virtual reality to check that we are able to assemble the product, that the parts fit correctly, and that the perceived quality matches our expectations. For small series production, the other advantage is the ability to work on the specificity of a product.
Patrick BAERT: Virtual reality allows a platform manufacturer to design a machine and have its design choices approved before moving to a physical prototype.
Creating new and more accessible and personalized training tools:
Patrick BAERT: Nowadays, training is one of the main uses of virtual reality. We can train operators on an assembly line before the factory is even built. Virtual reality also facilitates the professionalization phase. A welder in the industry can train, do as many virtual tests as he wants to improve his skills. He does not need to be in a workshop or to use components for this training. This saves time and productivity. It should be noted that the final test will obviously be done in real conditions.
Frédéric BORREL: Internally, we use it a lot for training. For example, we now sell electric trucks for which maintenance is not the same as for a truck running on petrol. Technicians must relearn part of their job. With virtual reality, we can train them to carry out maintenance actions in complete safety and all over the world.
Patrick BAERT: In my opinion, the other added value is to virtually test difficult situations and to educate on safety rules. In Haulotte’s case, we can imagine that in the future we will also be able to simulate the behavior of the MEWP, when it is deployed and subjected to a very strong wind for example. For this, the calculation model will obviously have to be adequate.
Frédéric BORREL: Finally, Augmented Reality can be used for remote assistance by providing information in real time to an operator on a production line. It is more practical and interactive than a screen on the line or printed documents.
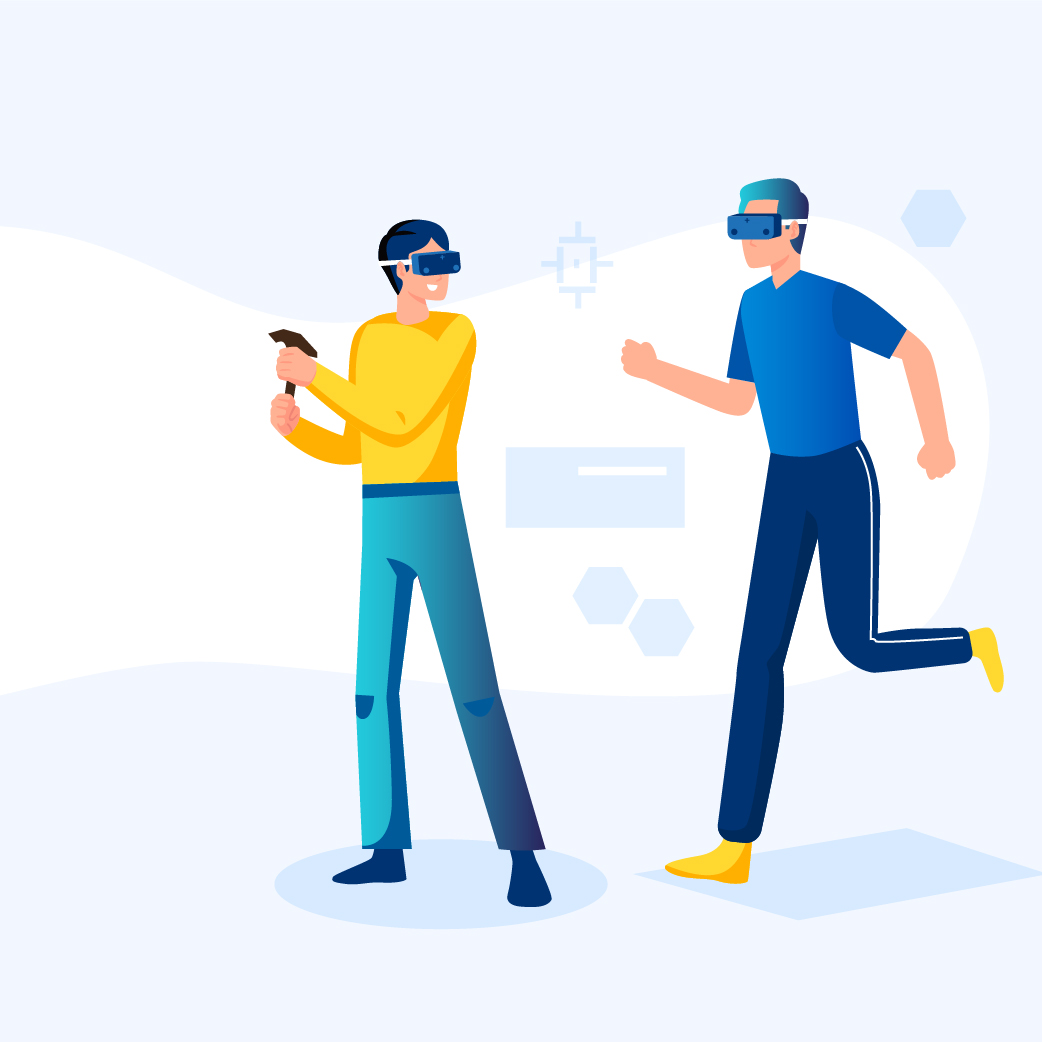
What about the impact on productivity and marketing?
Frédéric BORREL: Currently, the impact on productivity remains limited. Augmented reality is not yet popular because there is not yet an ideal device that is safe enough. Virtual reality is more mature. It has been used in the aeronautics and automotive industries for more than 20 years. Products are now of better quality, computers are more and more powerful to allow more complex simulations, with more realistic materials and light effects calculated in real time.
Patrick BAERT: I would add that virtual reality has become very common among large industrial clients, but still relatively little among their suppliers and SMEs because of the cost of entry into this technology (hardware and mostly human).
Frédéric BORREL: In the future, thanks to artificial intelligence, quality control could be done in real time to avoid further manual rework at the end of the line. This will improve the « time to market ». Augmented reality will also lighten the cognitive load of operators. For some tasks, they must learn and integrate a lot of information to be efficient. With augmented reality, the information will not need to be learned but will be sent at the right time. Operators will be able to focus on their job without having to integrate many references.
Patrick BAERT: These new technologies have already proven their effectiveness. Bugatti, the carmaker, announced that it has reduced by three the time it takes to design a vehicle between two prototypes and has cut the design budget by two-thirds.
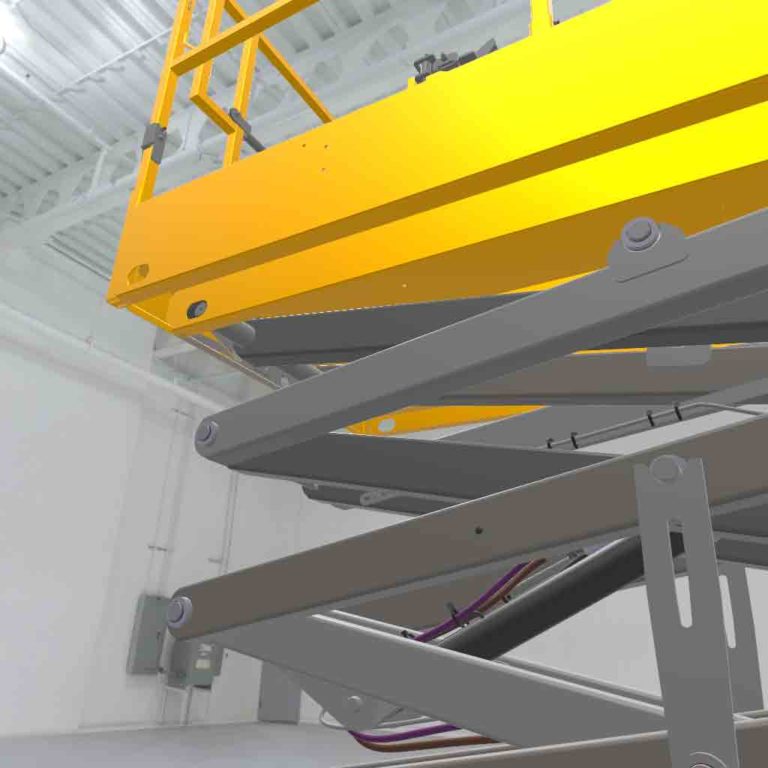
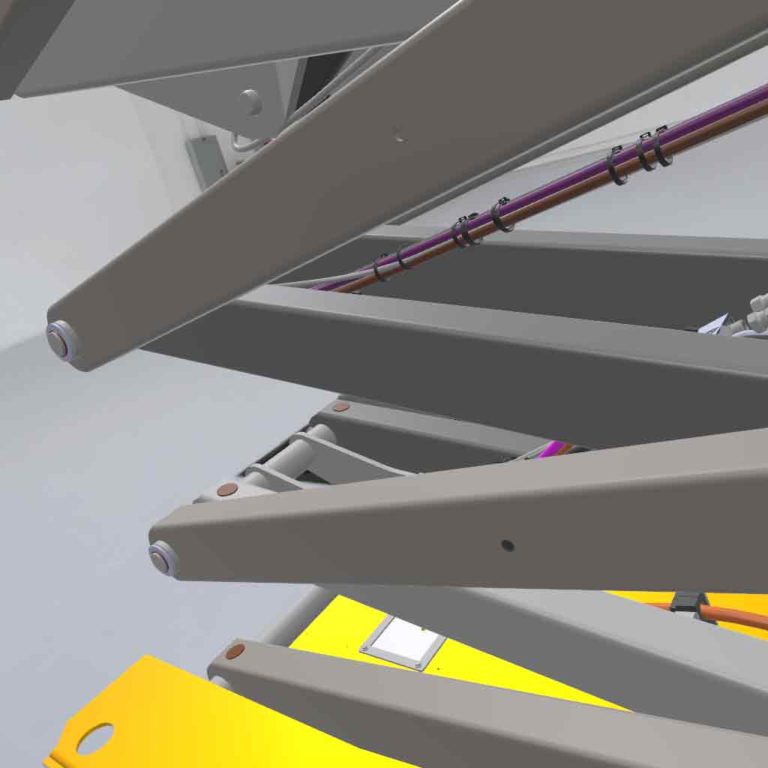
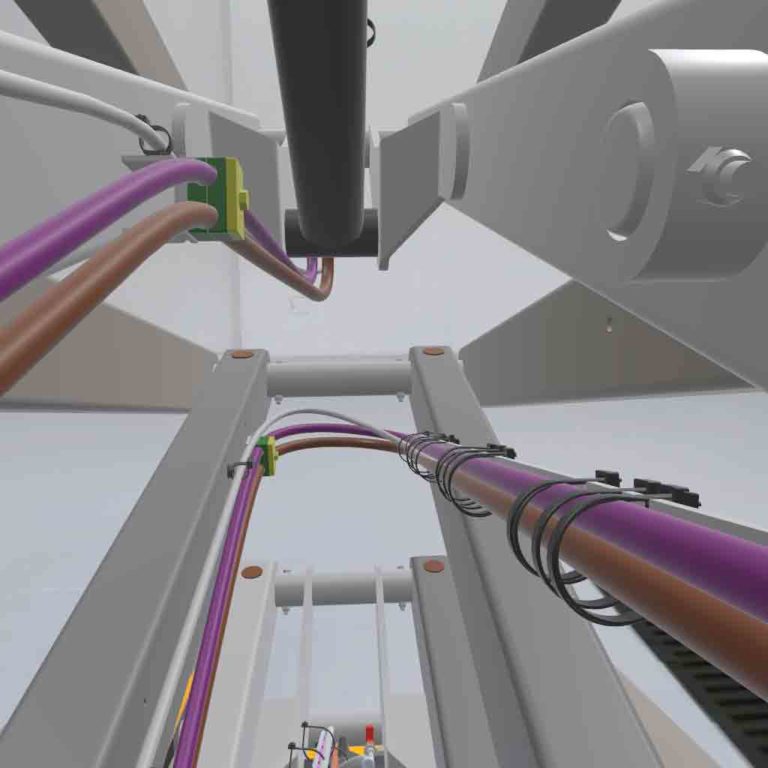
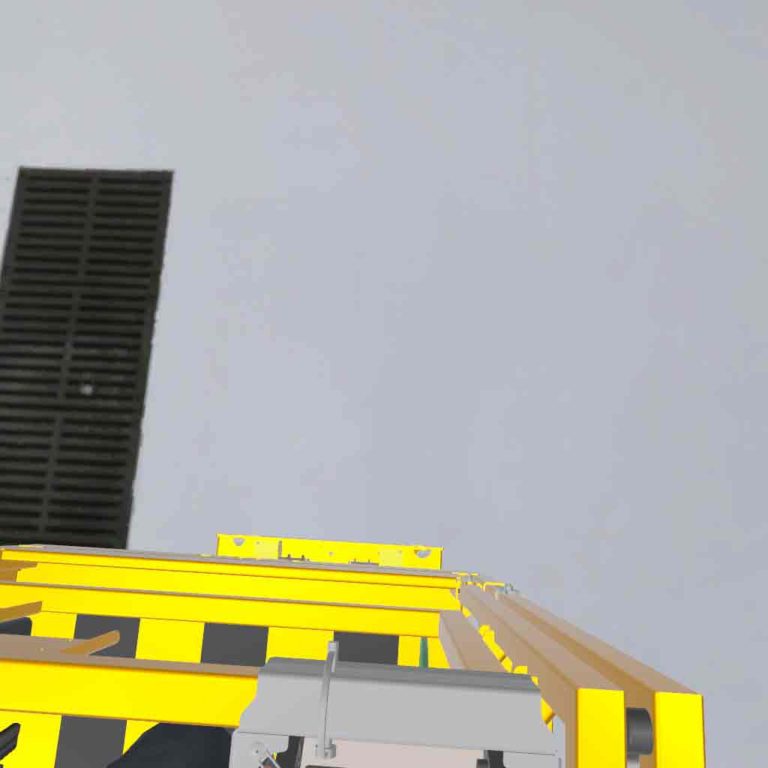
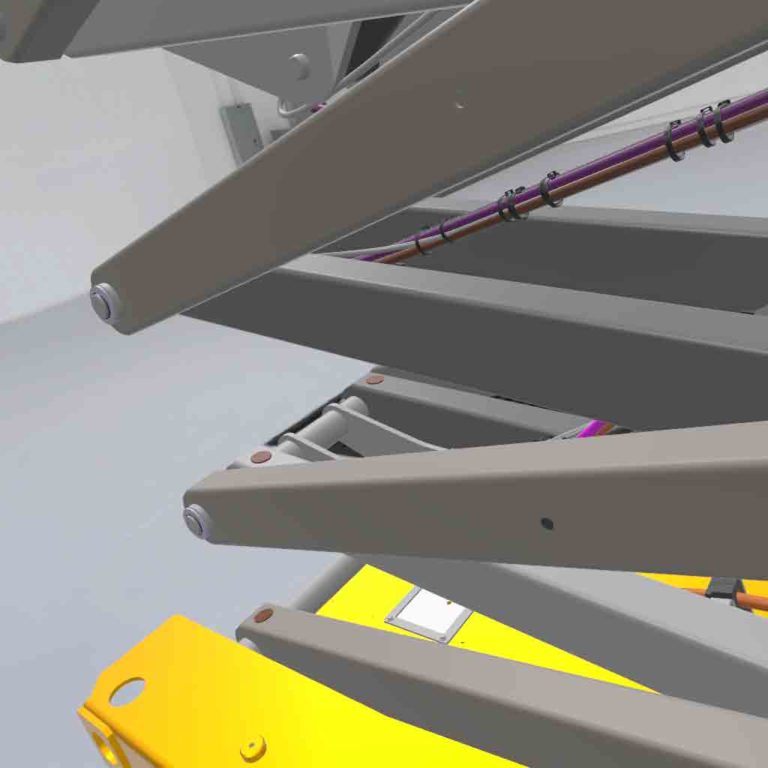
What applications can still be imagined in the future?
Frédéric BORREL: It will take some time before augmented reality is widely implemented in the industry, but it will really improve industrial manufacturing processes and product quality. It’s a revolution in the making.
Patrick BAERT: It is possible to imagine some metaverse type of applications, offering virtual universes with interactions. We can envision a workshop or a factory, with machines connected and controlled remotely. This real production universe will be cloned in virtual reality. Several people will be able to go there and exchange, intervene on the industrial process wherever they are located in the world. In the future, virtual reality could also involve other senses, such as heat feeling. We could then visit a building with a thermal feeling according to sun exposure, degree of isolation. In the industry, it will be possible to simulate the smell of the machine when it turns on, the noises it emits. The accuracy of this type of interaction is one of our areas of research. But it will not be done for another ten years or so.
What are the limits of virtual reality today?
Patrick BAERT: The biggest limit is the time usage. These days, a virtual reality helmet can be used for a maximum of 20 to 30 minutes, afterwards there can be side effects such as fainting. Virtual simulation is a representation of some form of reality. There is always a sensory bias, and our brain perceives this difference between true reality and virtual reality. After a virtual reality session, it is necessary to readapt to the real world.
Frédéric BORREL: We need to work on the acceptability of virtual or augmented reality devices. There are of course physical limits but also technological ones. Perfect augmented reality glasses do not yet exist. The other limit is the integration of these tools into information systems, to connect these devices to larger databases. We are only at the beginning of the adventure.
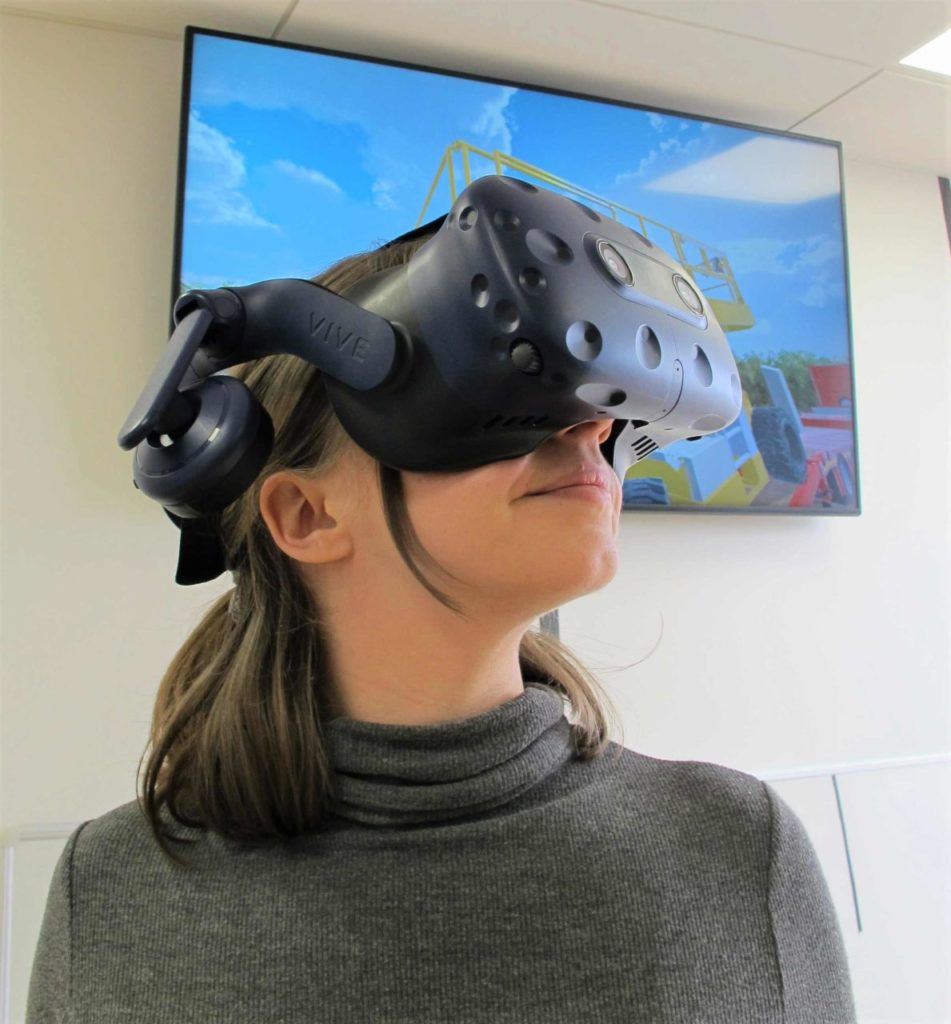
Promoting virtual reality technology into the industry
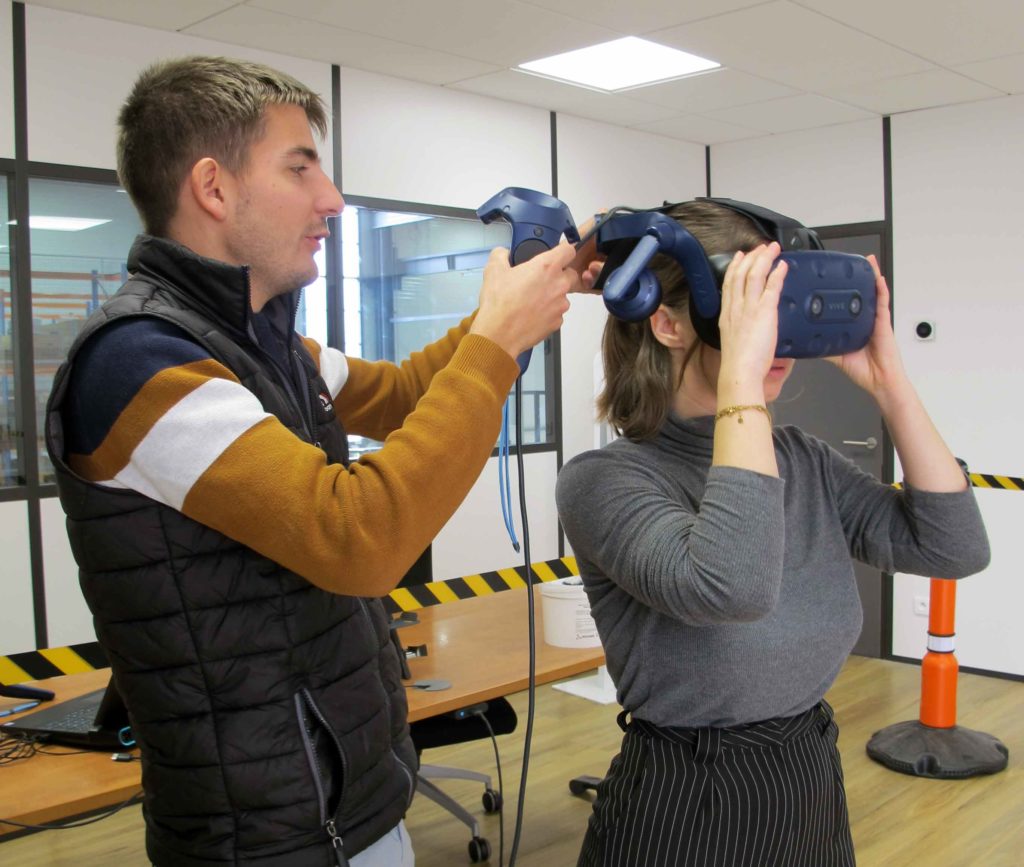
Frédéric BORREL defines himself as an « evangelist » of virtual reality. To spread this technology and popularize its uses, he is part of the Ruche Industrielle, a collective of companies in the Lyon area, which allows industrials to exchange on innovations and new technologies.
Frédéric BORREL has created an XR circle, dedicated to virtual and mixed reality, with Antoine Navarro, virtual reality engineer at Haulotte. For example, in June 2022, the organization held the XR Days, two days of equipment demonstrations, conferences, use case studies and experience sharing with representatives from Haulotte, Volvo-Renault Trucks, Airbus Helicopters, Renault Group, Transdev, Boehringer, etc., and with a presentation by Patrick BAERT.