Haulotte has modernized its electric scissor lift Compact range for a better and more complete user experience. This range provides a work enveloppe from 8-to-14-meters for indoor and outdoor activities, featuring the latest Haulotte technologies. They are even more robust and maneuverable. Interview with two designers involved in the project: Baptiste Roland, marketing product manager, and Jean-Yves Charrier, project manager.
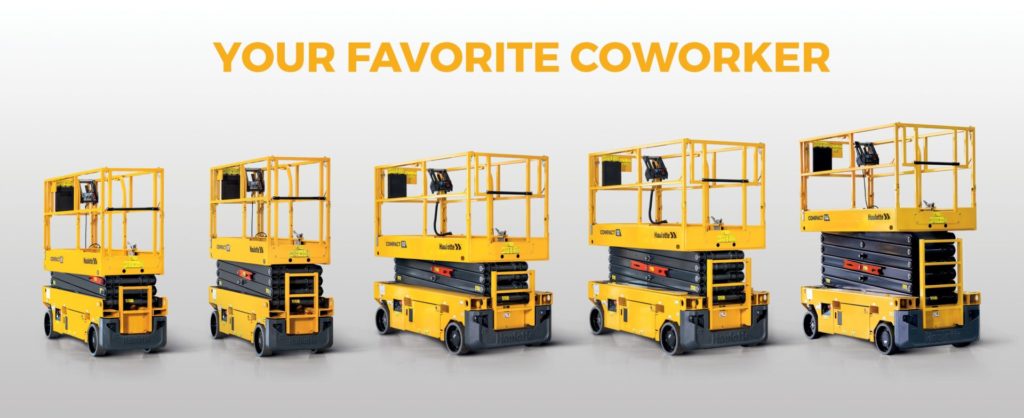
What are the key features of these new Compact electric scissors? How are they standing out from the previous Compact Range?
Baptiste Roland: This new compact range of scissor lifts is equipped with non-marking wheels, that can carry 1 to 3 workers at the same time. It has a higher load capacity (between 250 and 450 kg) and an extra reach feature that goes up to 8-to-14 meters in height. On top of this, those are very compact machines. They can circulate in tight spaces through doors or corridors.
They are mainly used for “maintenance” type of work, finishing work, building maintenance, or even for stock management. They are « slab » models, which move and circulate on stable, smooth, and flat ground.
Right now, compact range scissor lifts are the most sold solutions all around the world. They have very impressive sales volumes, especially for Haulotte. We call it a « runner », a go-to product when in need of a MEWP.
Why did Haulotte want to refresh its compact range of scissors lifts?
Baptiste Roland: I think the range was great for a long time, but it needed to be modernized so it won’t become outdated. It was launched back in the early 2000s. Despite many updates, its design and its technologies needed to be refreshed based on what we would find on the market. It is a very competitive industry with strong international key players, especially in China. We had no choice but to rethink this range to maintain our position and reaffirm our vision.
Jean Yves Charrier : We had to bring our solutions up to the brand’s quality and service standards. We also had to align ourselves to the latest safety and governmental regulations. It was a big project, which meant at the time that we had to team up with a few people across the company. We were all involved: from the marketing team, the design office, quality, service, after-sales, and purchasing, to the regulations department, as well as our two factories in Reims and China with the procurement, industrialization, and quality department.
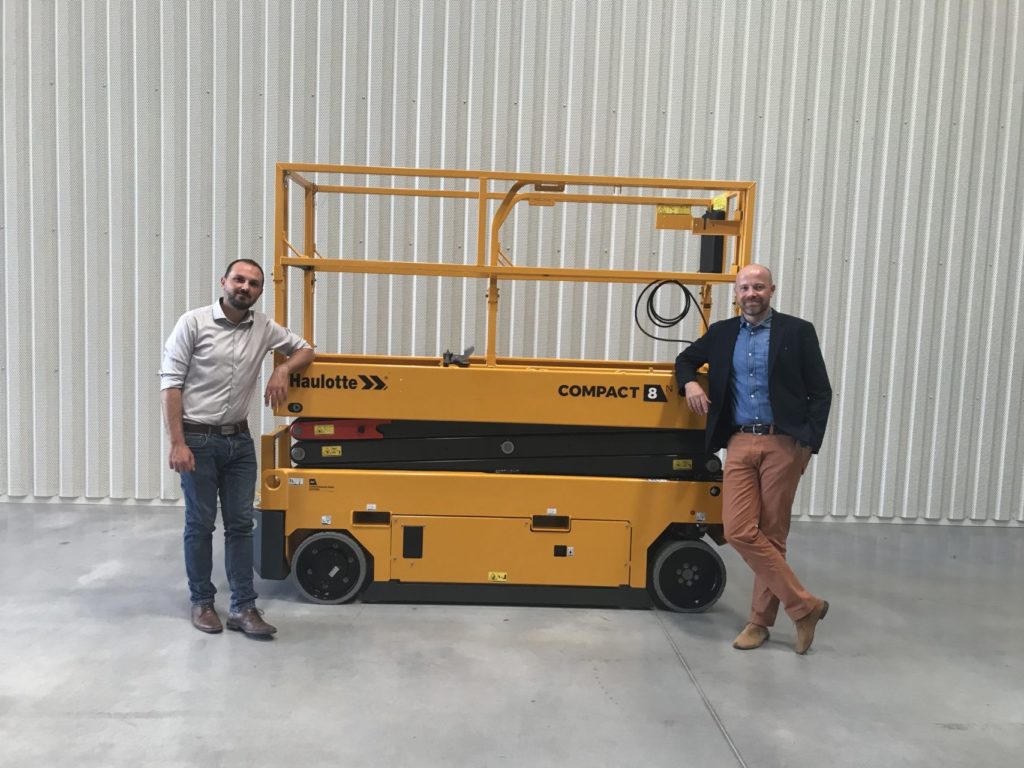
What are the main innovations?
Baptiste Roland : We have completely reworked the electronic structure with CAN-BUS. Part of the system modernization includes better energy and battery management thanks to Haulotte Activ’energy management system and our Smart charger, integrating intelligent user interfaces with Haulotte Activ’Screen system, and increasing the solution’s ergonomics by developing intuitive controls that will limit piloting errors. There’s also an optional anti-crash feature.
Additionally, users can now climb outdoors without reducing onboard load. It is a big time-saver. The motorization of the compact range is entirely electric and asynchronous. It is no longer hydraulic. From a movement point of view, it is way smoother. It also reinforces users’ safety and avoids product deterioration. Finally, this range is compatible with our Sherpal telematics solution, which means that the compact machines can be located, and breakdowns diagnosed – even remotely!
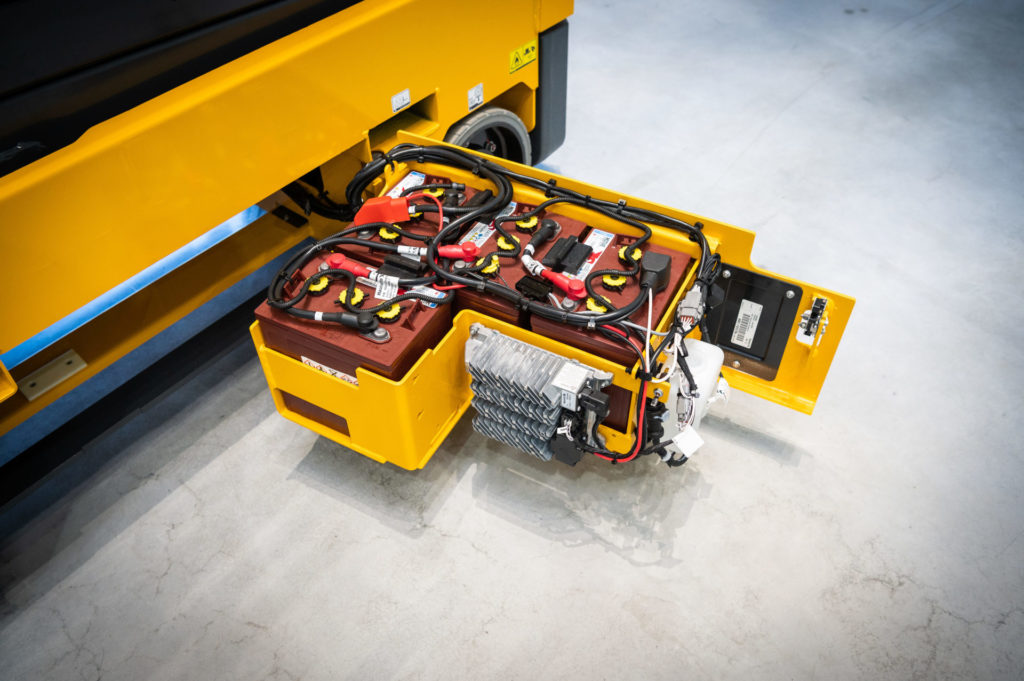
Jean-Yves Charrier: This range is now up to Haulotte standards. We have reinforced its robustness by integrating new components so that the machines could be used for every site, even on the toughest ones.
We also have focused on deflection and the roll that can occur when at full height. We wanted to perfect our system as much as possible to warrant a safer and optimized user experience, both at height and outdoor with bigger load capacity. It was a big redevelopment project and a real economic challenge for us to keep the cost as low as possible.
Was robustness essential for you when working on redesigning the compact range?
Baptiste Roland: It was. For the first time, we have used our new internal Design Guideline process 100%. We wanted to create a machine that will be recognizable at first glance. So, we designed one with a robust appearance, strong-looking without being too heavy. To do so, we had to reshape the platform plinths and the chassis, the handles ergonomics, the access to the ladder, the step, and the integrated screen which is now visible when working in a standing position…
Today, we have a brand-new range of scissor lifts that exceed the standards of our competitors.
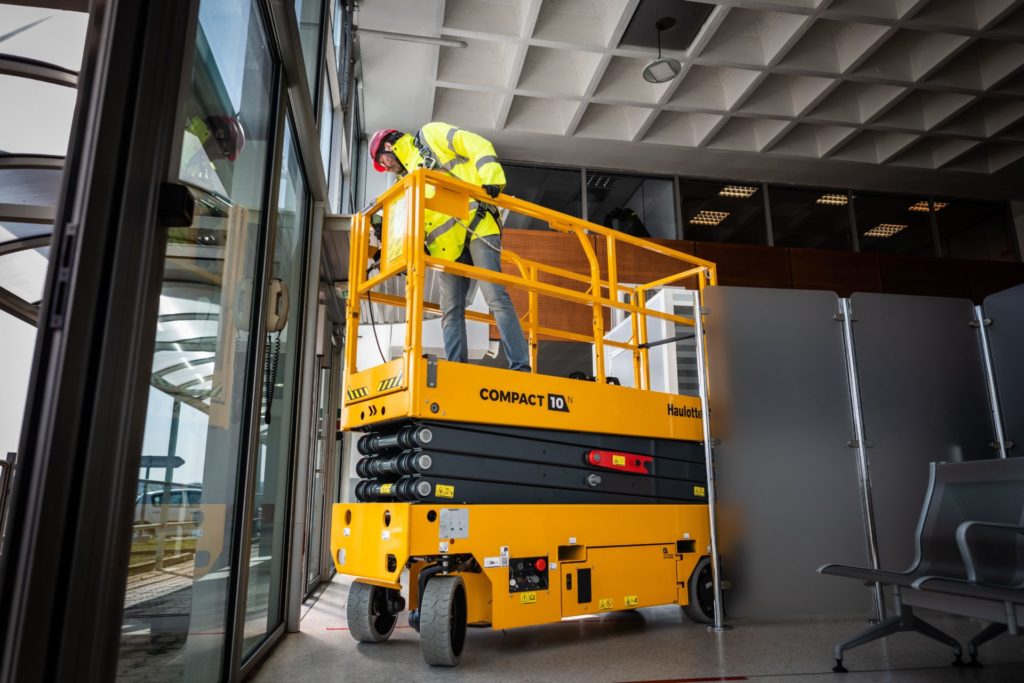
How did your customers help you redesign this new range?
Baptiste Roland: Over the past two years, we did a lot of preparatory work with our customers to know what their expectations were and see how they saw themselves with this new range. We have been very attentive to their opinion throughout the entire redevelopment project, using augmented reality models, reviewing technical data, checking prototypes, and finally, having them test machines. Both customers, their managers, and the end-users helped us improve many things. For example, they highlighted the low quality of certain components, their design, and their location in the machine. They pointed out certain practices that operators have on a daily basis, which allowed us to adjust ourselves.
Jean-Yves Charrier : Each market has its specificities and demands so it was very interesting to hear everyone and work with our clients. In China, for example, our customers were sensitive to the aspects of robustness and the protection of sensitive systems. Part of it is because these machines are used intensively over there. The Chinese market also wanted batteries with a minimum of maintenance or specific plugs. It must be known that our solutions can be personalized by zone or by country. Korea, for example, requires a third flashing light. So, at certain points in the design process, we shared our progress with our customers. At the end of 2019, we were supposed to go to China to present our models, but the pandemic and the lockdowns forced us to be imaginative and changed our initial plans. So, we did organize calls with our foreign customers to present to them our 3D models using virtual reality.
How did you deal with the challenges of the pandemic?
Jean Yves Charrier: The successive lockdowns, the hazards related to supplies issue, the current geopolitical situation in Ukraine… it obviously had an impact on the launch of the new compact range. It has caused a few months delay on the initial planning. Both of our factories (one in Reims for the European and American markets and one in Changzhou for the Asian-pacific market) are still affected by these problems. It’s a daily struggle and we had to look up for new sources of supply. However, we were very fortunate because after a few tests, we got positive feedbacks from our clients – mostly on our products robustness, its seating and its handling.