MEWPs (Mobile Elevating Work Platforms) are considered to be lifting equipment. As with all worksite equipment, proper care and maintenance can guarantee you and your customers optimum performance and operator safety. As such, they need to be inspected when they are put into service, periodically, and when they are put back into service following repair or modification. Load calibration is one of the most important points to check, ideally once every 6 months.
What does overload mean?
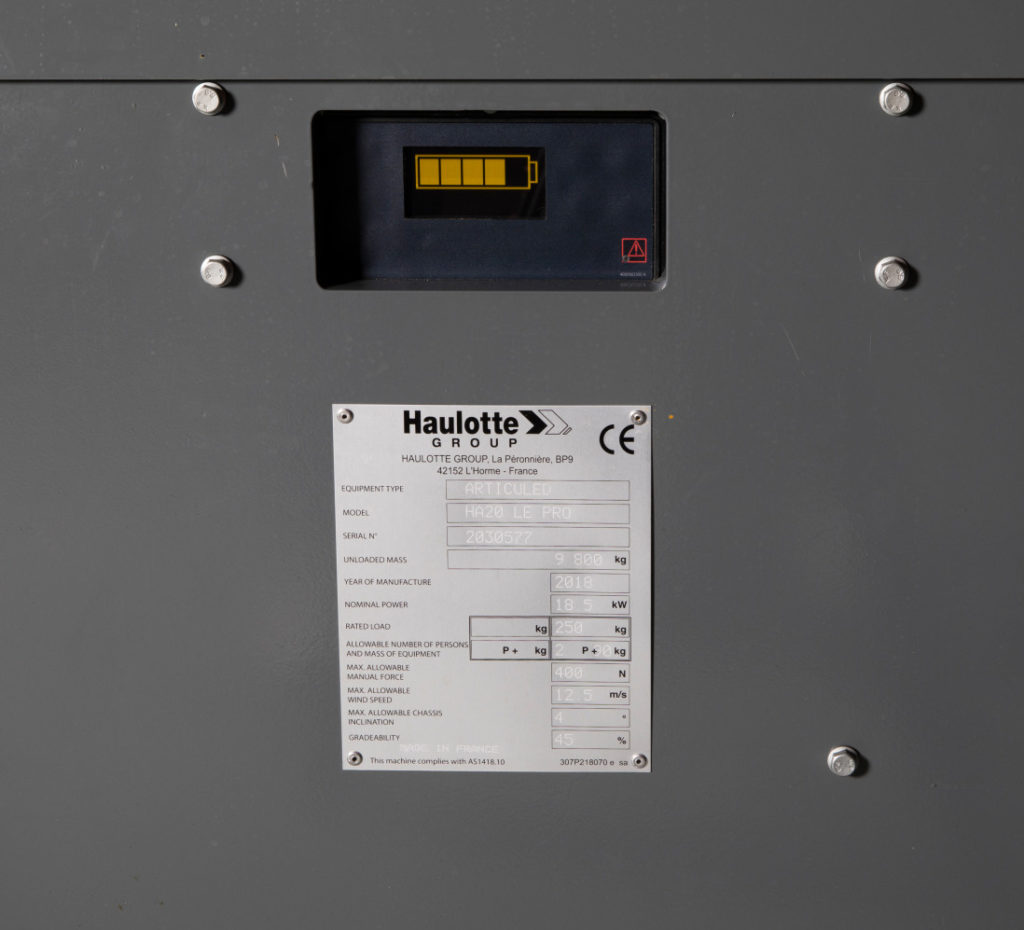
The basket or platform overload system is designed to stop machine operation if the load capacity has been excedeed. The machine load capacity is always indicated on the « manufacturer » plate and riveted to the chassis.
Operating a MEWP despite overload warnings can, in the long term, make it impossible to correctly assess the load on board.
Operator safety is intrinsically linked to machine stability, which could be compromised if the overload is incorrectly assessed, potentially causing the machine to tip over.
What is the purpose of load calibration?
The purpose of this process is to check that the basket’s overload system is functional, that it accurately assesses the weight loaded in the basket or platform, and that it correctly detects any overload and warns the operator.
When should load calibration be performed?
- During maintenance and periodic inspections,
- If you have purchased a used aerial work platform, before using it for the first time in a working situation,
- After changing or repairing a component of your aerial work platform that plays a role in load calibration (in this case, load calibration is included in the assembly instructions for the replaced part or component),
- If the MEWP fails to lift its maximum rated load, indicating this problem by means of an alert or fault code on the control panel.
How do I calibrate?
In all cases, regardless of the manufacturer, the load calibration method is detailed in the maintenance manual and depends on the MEWPs model. Depending on the model and on-board technology (pressure angle and strain gauges), several methods are available, including « static » and « dynamic » tests.
#1: For systems using strain-gauge technology
A static test, in which the machine is subjected to several levels of load:
- A no-load calibration test
- A calibration test with a variable weight ranging from 75 to 300 kilos
- A calibration test with maximum rated load
#2: For systems incorporating angle pressure technology
A static test in which the machine is subjected to several load levels, including its maximum working load. Weights are placed in the basket or platform, and the machine is held in the lowered, folded position. During this test, the ECU will check the on-board weight vs. the perceived weight using the strain gauge.
A dynamic test in which the machine is made to bear its maximum working load in all elevation positions, including full height. The angle sensors on the arms and cylinders will evaluate a pressure angle, enabling the on-board weight to be calculated.
A few tips for successful calibration?
#1: Perform operation indoors
Perform the operation indoors, in a workshop. This will eliminate wind, which could falsify the calculations during the dynamic tests. Another advantage is that you may be able to use a lifting ramp to place the weights in the basket or platform.
#2: Know value of weights
If possible, use calibrated weights with exact known values.
#3 Check calibration process
To check that calibration has been carried out correctly and accurately, you can place a weight whose value you know in the basket, then use the on-board diagnostics tool to launch the « Estimated Load » process, which checks the weight loaded in the basket. If the weight indicated is equal to the value of the weight you placed in the basket, then the load calibration is successful.