Haulotte launches two new electric articulating booms: SIGMA 16 and SIGMA 16 PRO, designed to be productive, agile, comfortable, with reduced maintenance costs.
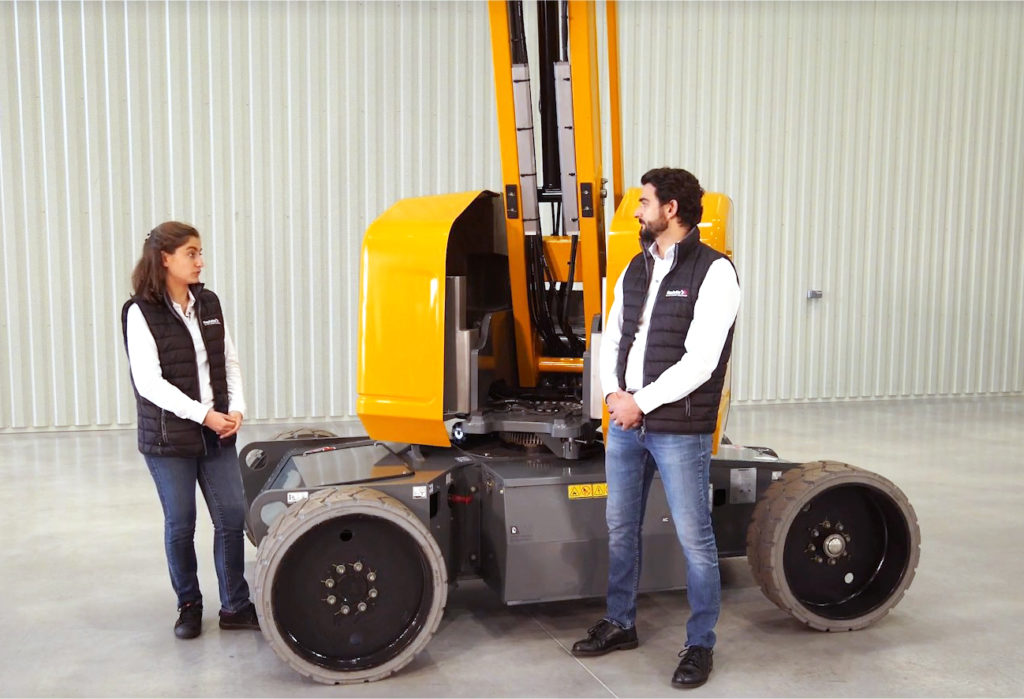
Eugénie Viard-Gaudin, product manager and Benoit Baleydier, project manager, reveal the project’s secrets.
What was the genesis of the SIGMA 16 project?
Eugénie Viard-Gaudin :
It was the renewal of an existing machine that was reaching the end of its life cycle. It is a vital machine in our range, an articulating boom for stabilized slab floors, which has been on the market for more than 15 years. The objective was to bring it up to Haulotte’s innovation and safety standards. But this is not an update. We started with a blank sheet of paper and designed the SIGMA 16 with a new architecture.
Benoit Baleydier :
The objective of this project was to design a versatile platform because the machine must be able to respond to multiple applications, and agile because its architecture maximizes its working envelope by making the machine as efficient as possible. It was also essential that the platform be compact to work in a congested environment such as a warehouse and outdoors on stable ground. This data is the crucial criterion for our customers looking for an efficient and simple machine.
What were the design criteria for this new platform?
Eugénie Viard-Gaudin :
We wanted to make the SIGMA 16 the most productive machine possible, but also to offer the best working envelope on the market, i.e., the best compromise between working height, outreach and articulation point. Our challenge was to give it maximum movement while having the turret, the counterweight, in the chassis envelope. This machine’s real advantage is to combine two movements to reach faster a working area. We have also introduced a jib with horizontal rotation, a novelty in this segment. The jib can move horizontally to access certain areas more quickly and gain the last 50 cm. All of this allows faster and more efficient access to the work area and improves productivity. Of course, we have considered the user’s need for comfort by reducing jolts in the basket.
Finally, we have also optimized serviceability to reduce maintenance costs, increase availability and meet our customers’ expectations. For example, components are easily accessible through covers that open wide without tools. We have also done a lot of design work on routing, with hydraulic and electrical hoses that are easier to read and simpler to maintain or change.
Benoit Baleydier :
The strength of the project here was to integrate the needs cited by Eugénie and to integrate them from the start of the project. To do this, the design office teams worked on the machine’s digital modeling well upstream in the design. We validated that the machine met the needs through these tests while complying with the applicable standards. That allows us to identify the challenges to meet very early on.
What are innovations from Haulotte DNA available on SIGMA 16?
Benoit Baleydier :
SIGMA 16 have the security innovations of the RTJ range. It includes the Haulotte Activ’ Shield Bar, the anti-crushing system for improved safety at height, and the Haulotte Activ’ Lighting System, LED lighting to facilitate loading and unloading in low light conditions. Finally, the SIGMA 16 offers Haulotte Activ’ Energy Management, an innovative solution combining an intelligent charger as standard with centralized battery charging options. This equipment is standard on the SIGMA 16 PRO and optional on the SIGMA 16. Haulotte Activ’ Energy Management reduces costs for customers and lowers TCO (Total Cost of Ownership). Indeed, batteries can be large expense items if they are poorly maintained.
This project was, above all, a team effort. How did the development of SIGMA 16 take place under the conditions of the health crisis?
Benoit Baleydier :
The project team was about ten people from several departments: purchasing, quality, marketing, design office, regulations, industry, logistics, research and development, test center… Most of the company’s departments took part in this project, right up to our factory in Romania, where we made several return trips, when possible in 2020. Some reviews were done on the machines by videoconference during the containment periods. For example, we validate the path by Visio between Romania and France. This period was a real challenge, but the teams always proposed solutions. We reinvented ourselves enormously in our working methods.
Eugénie Viard-Gaudin :
Because of the health crisis, the training of the sales and technical teams was done remotely, by video. The project team was very involved since we were the video training modules’ actors. We had to be creative. Team members explain their role in the project. Some contributed to the presentation in detail or demonstrated their expertise in front of the camera. It was an enriching experience because the project teams had not been very involved in the training until then. Everyone could explain their job, get out of the shadows, and out of their comfort zone. It’s a great human adventure.