While preventive and predictive maintenance activities play a vital role in ensuring the prolonged well-being and efficiency of mobile elevating work platforms (MEWPs), there are instances when the machinery experiences malfunctions. In such cases, swift response becomes imperative to address the immediate situation.
Before solving the problem, you need to be able to identify the fault, defect or incident that has occurred, thanks to the fault code and the information it indicates. To troubleshoot the machine yourself, or to pass on precise information that will enable the technician to intervene, you need to know what a fault code is, where it is indicated, and on what documentary basis you can carry out maintenance.
Find out the answers to these questions in this article. If you would like to find out more, and in the event of a breakdown, contact the Haulotte sales network and our Haulotte Service teams.
What is a fault code?
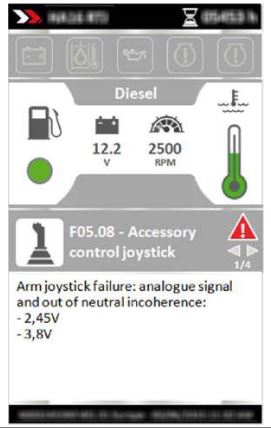
Every MEWP is equipped with an on-board fault detection system, which indicates the type of fault to the operator. According to the type of fault, the machine may switch into downgraded mode and certain movements are prevented to maintain Operator’s safety. A machine with a fault code must not be used until the problem has been solved and the code has disappeared.
Fault codes are digital codes, they are employed for diagnosing problems in a machine. Every fault code is unique and corresponds to a particular malfunction, incident, fault or defect, whether it is a generic issue or a manufacturer-specific error. A fault codes offer more detailed information than a machine alert or indicator symbol, such as engine light in our car can provide. Fault codes can thus provide more detailed information than a simple LED, for example, they can clearly identify the component block on which the fault is located, or in some cases the part(s) to be repaired.
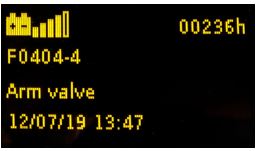
On Haulotte equipment the fault code always starting with a “F”. It is composed of several numbers or letters, for example: “F06.01” is a fault code that indicates with the load management system and more specifically, that the load calibration must be carried out according to the maintenance procedure.
Where to find the fault code?
Lower control box or Haulotte Activ’ Screen: The first place where the fault code is displayed is the lower or ground control box. On newer machines, the control box is equipped with a display named “Haulotte Activ’Screen” that provides essential information on machine status as fault codes.
Haulotte Activ’Screen is an on-board diagnostic tool which help the technicians to manage daily machine maintenance, adjust the parameters and perform diagnosis.
Thanks to Haulotte Diag App: The Haulotte Diag application can also be used to obtain more information on the fault code, enabling users to make a precise diagnosis of the fault and find the best way to solve it. Haulotte Diag works in conjunction with a wireless VCI box (Vehicle Communication Interface).
Technicians have remote access to program, troubleshoot, calibrate, and generally diagnose all Haulotte machines using Wi-Fi wireless technology. Haulotte Diag is available in 12 languages and includes advanced troubleshooting features displaying the whole process to resolve the problem: information about the probable cause of the failure, instructions to solve the problem, components to check and status in real time, diagnostic instructions, locations and pictures of components.
Thanks to SHERPAL telematic solutions connected to your MyHaulotte account: MyHaulotte portal gives simplified access to all the services and resources associated to Haulotte machines. Fault codes are part of the data managed by the portal. For all machines associated with a profile or a fleet, it is possible to identify active fault codes, as well as accessing the history of oldest and resolved fault codes.
On the portal, you can also consult the recurrence of a fault code. The history allows you to see whether the fault code recurs cyclically or is a one-off. This information makes it easier to detect a component reaching the end of its service life, or misuse of the machine by operators. Fault codes are classified by severity and type, enabling them to be filtered and classified.
How to resolve and clear a fault code?
A fault code will remain uncleared until the underlying issue is resolved, and the machine is brought back to a state of proper working condition.
If you are planning to troubleshoot yourself, you first need to find all MEWP documentation to get information and identify what to maintain or fix. To achieve this, Haulotte Service have created a technical search engine named “ETI LITE”. Accessible 24/7, this virtual library stores all documentation related to the maintenance and repair of Haulotte aerial work platforms and telehandlers. Easy to use, you only need to enter the machine’s serial number to consult the documents.
If you still need support and help make a repair, you can contact our call-center for a rapid online troubleshooting. Our technical advisers are available to assist you during extended time slots and provide you with technical assistance and personalized support.
In case where on-site repair needed, you can count on our mobile technicians, anywhere in the world. You can book a consultation by contacting one of the 21 Haulotte subsidiaries or by reserving a slot directly on your MyHaulotte account.