In a sector where machines evolve as rapidly as the technologies that equip them, maintenance training has become a strategic imperative. Bruno Monglon, a maintenance training instructor and WorldSkills expert, has been embodying this commitment to excellence, transmission, and innovation for several years. Drawing from his experience in international competitions, he shares his vision of best educational practices and the pivotal role of companies like Haulotte in transforming the profession.
An integrated approach: equal parts theory and practice
The advantage of global competitions like WorldSkills is that they provide the opportunity to experience a wide range of pedagogical and practical training methods. Abroad, certain approaches have particularly caught Bruno Monglon’s attention: « Switzerland and Canada: countries where corporate learning is combined with high technological standards. »
Bruno has had the opportunity to discover numerous pedagogical methods during international competitions and exchanges and highlights the exemplary Swiss model: « What inspires me is their ability to closely link practice and theory. Swiss champions dominate the competitions because they emerge from both companies and schools with skills rooted in reality. »
This model could serve as inspiration for some training centers in France, where the gap between training and on-the-ground work can sometimes be felt: « There is a real gap. We could learn from their scheduling, their programs, and their way of involving young people from the start in demanding professional practices. «
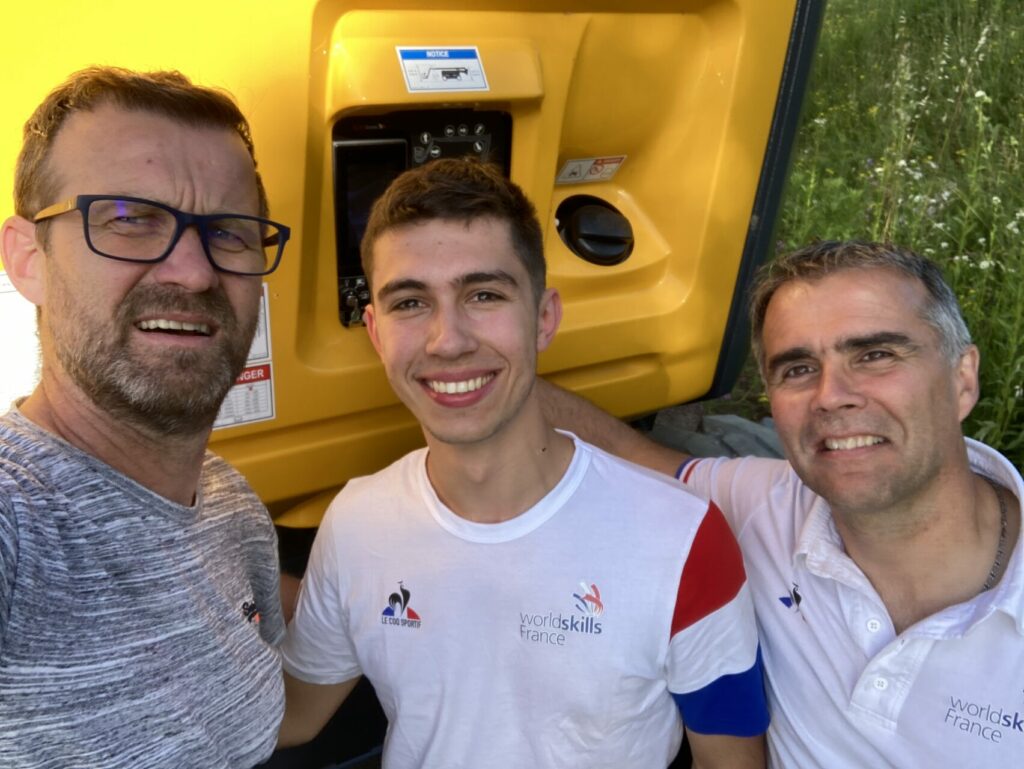
In France, he commends the quality of vocational high schools, but especially the decisive contribution of manufacturer training centers, which are highly specialized and allow trainees to develop specific skills and deepen their training.
WorldSkills: a showcase of the profession and a catalyst for vocation
For Bruno Monglon, international competitions are not just a technical challenge: « They spark wonder. Young people discover that their profession is noble, demanding, and recognized. It motivates them and gives meaning to their journey. »
Beyond the excitement, these events provide access to modern working methods they wouldn’t otherwise see. « I even have first-year students asking to train! It creates a real virtuous circle, » says Bruno.
Between electrification and digitalization: major challenges for training
Bruno Monglon discusses current challenges in the industry, particularly digitalization and electrification:
« Today’s machines combine thermal, electric, embedded electronics, high voltage… We need to invest more time, equipment, and resources to cover all these aspects in training. »
The introduction of high voltage, especially in lithium batteries, raises questions about safety and specific certifications: « We will have to quickly adapt our practices to stay grounded in the realities of the profession, » emphasizes Bruno.
Skills shortage: multi-level responses
The consensus is clear: the sector is lacking trained personnel. To address this, Bruno Monglon advocates for progressive and complementary training paths:
- Vocational training from high school to gain practical experience
- BTS for technological skill advancement
- Post-diploma targeted training such as Local Initiative Complementary Training (FCIL) or Professional Qualification Certificates (CQP)
« These programs are invaluable. They respond to very concrete field needs, and we are planning to open a new FCIL at the start of the school year in our high school, » says Bruno.
Role of companies: engines of transformation
Haulotte and other industrial players have, according to him, a central role to play: « The presence of industrials at WorldSkills competitions changes the game. It’s a showcase but also a laboratory: we observe, we exchange, we progress, » recalls Bruno.
He advocates for early involvement, starting from the preparation phases, but also for regular material and educational support: « Companies have both resources and valuable expertise. By working with us, they help an entire sector progress. »
Bruno Monglon cites the example of the Evofia initiative (supported by France 2030), where high schools and industrial companies collaborate to train teachers and enhance student competencies: « It’s an excellent initiative. If manufacturers join forces, they can genuinely transform practices. »
The initiative aims to train up to 15,000 recruits by 2030.
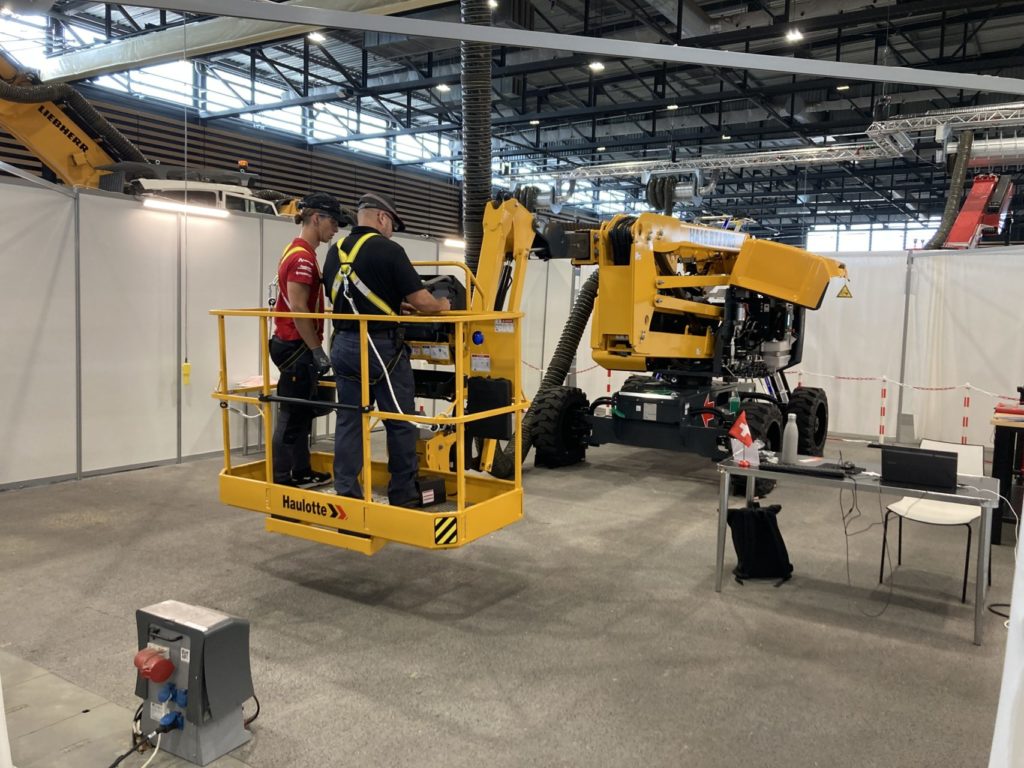
Why not go further by facilitating international mobility? Bruno comments: « France–Canada exchanges, for example, with young people spending a month abroad and returning enriched. It’s the kind of project that could truly move the needle. »
Passion as a lever, cooperation as a driver
Bruno Monglon embodies this strong conviction: training is a continuous commitment. To respond to the sector’s transformations, it will take committed educators, adapted training, engaged industrial partners and motivated young people from the very start.
Bruno emphasizes: « The future of maintenance lies in our ability to work together. So let’s focus our energy on the right things. »